Just How Plastic Injection Molding Drives Performance in Automation
Just How Plastic Injection Molding Drives Performance in Automation
Blog Article
Comprehending the Fundamentals of Plastic Shot Molding Procedures
Plastic injection molding serves as a foundation of modern-day production, providing a systematic method to producing intricate elements with precision. Discovering these crucial elements could reveal exactly how even small changes can lead to considerable renovations in production results, raising questions concerning the potential for innovation in this well-known process.
What Is Plastic Shot Molding?
Plastic shot molding is a commonly utilized manufacturing procedure that transforms thermoplastic and thermosetting materials into specific and complex forms. This technique is favored for its capability to produce high quantities of similar parts with outstanding accuracy, making it a crucial technique in various markets, consisting of auto, customer goods, and clinical devices.
The process entails thawing the chosen plastic material and injecting it into a mold under high pressure. The mold, made to the specifications of the wanted component, allows the molten plastic to materialize as it cools and strengthens. When the product has actually set, the mold is opened up, and the completed part is ejected.
Plastic shot molding offers numerous advantages, including decreased waste, uniformity in production, and the ability to integrate elaborate layouts that might be challenging with other producing techniques. Furthermore, it supports a broad variety of materials, each providing distinct properties that can be tailored for particular applications. As industries proceed to innovate, plastic injection molding continues to be at the forefront, allowing the growth of advanced products that meet evolving consumer needs.
The Shot Molding Refine
The injection molding process is an advanced technique that entails numerous vital stages to create premium plastic components. At first, plastic pellets are fed right into a warmed barrel where they are melted into a viscous fluid. This molten plastic is then infused under high pressure right into a precision-engineered mold and mildew, which shapes the product right into the desired form.
As soon as the mold and mildew is loaded, the plastic is enabled to cool down and solidify, taking the form of the mold cavity. Air conditioning time is important, as it influences the cycle time and the final residential properties of the shaped part. After enough air conditioning, the mold and mildew opens, and the completed component is expelled using ejector pins.
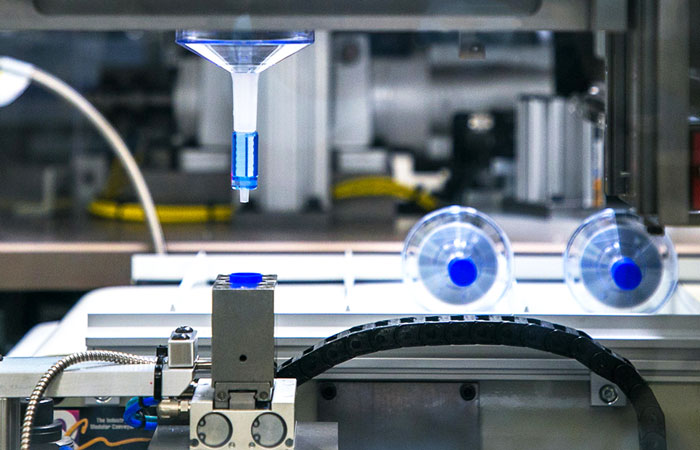
Products Used in Injection Molding
Numerous products can be used in the injection molding procedure, each offering distinct buildings that deal with certain applications. One of the most frequently made use of products include thermoplastics, thermosetting plastics, and elastomers.

Thermosetting plastics, like epoxy and phenolic resins, undergo a chemical modification during the curing procedure, leading to an inflexible, stringent framework. These materials are ideal for applications needing high heat resistance and architectural honesty, usually made use of in electric insulators and vehicle components.
Elastomers, including silicone and rubber-based materials, provide flexibility and strength. Their unique homes make them appropriate for applications that demand elasticity, such as seals and gaskets.
Furthermore, specialized materials like bio-based plastics and composites are gaining grip for their environmental advantages and boosted performance attributes, broadening the range of shot molding applications in different sectors. Understanding the homes of these materials is vital for selecting the suitable kind for details tasks.
Advantages of Shot Molding
Shot molding stands apart as an extremely efficient production procedure that provides numerous benefits for creating complicated components with accuracy. Among one of the why not try this out most significant advantages is the capability to produce complex layouts that would be challenging or impossible to achieve with various other approaches (Plastic Injection Molding). The process enables in-depth attributes and limited tolerances, making certain premium elements
In addition, injection molding is recognized for its rapid manufacturing capabilities, making it an excellent selection for high-volume manufacturing. When the mold and mildew is created, components can be generated rapidly, decreasing preparations and boosting total productivity. This performance not just reduces production prices yet also offers a competitive edge on the market.
The adaptability of materials made use of in injection molding additionally boosts its appeal. A broad range of thermoplastics and thermosetting polymers can be utilized, enabling makers to pick materials that best meet their particular needs, including stamina, adaptability, and warmth resistance.
Additionally, the procedure minimizes waste, as excess product can often be reused and reused. This sustainability aspect adds to a minimized ecological influence, making shot molding a liable production selection. Generally, the benefits of shot molding make it a preferred approach for numerous industries.
Aspects Influencing Product High Quality
While countless aspects can influence product top quality in injection molding, understanding these aspects is important for accomplishing ideal outcomes. Secret aspects include product option, refining criteria, and mold layout.
Material selection plays an important role, as different polymers display one-of-a-kind residential properties that influence flowability, strength, and thermal stability. Poor material selection can cause defects such as warping or incomplete filling.
Processing parameters, including stress, temperature level, and cycle time, should be meticulously managed. Variants in these settings can cause disparities partially dimensions and surface finish. Excessively high temperatures may cause degradation of the polymer, while poor pressure can result in brief shots.
Mold and mildew layout is equally vital, as it establishes the circulation of the molten plastic and the cooling procedure. Inadequately designed molds might result in uneven cooling rates, leading to dimensional mistakes and residual tensions.
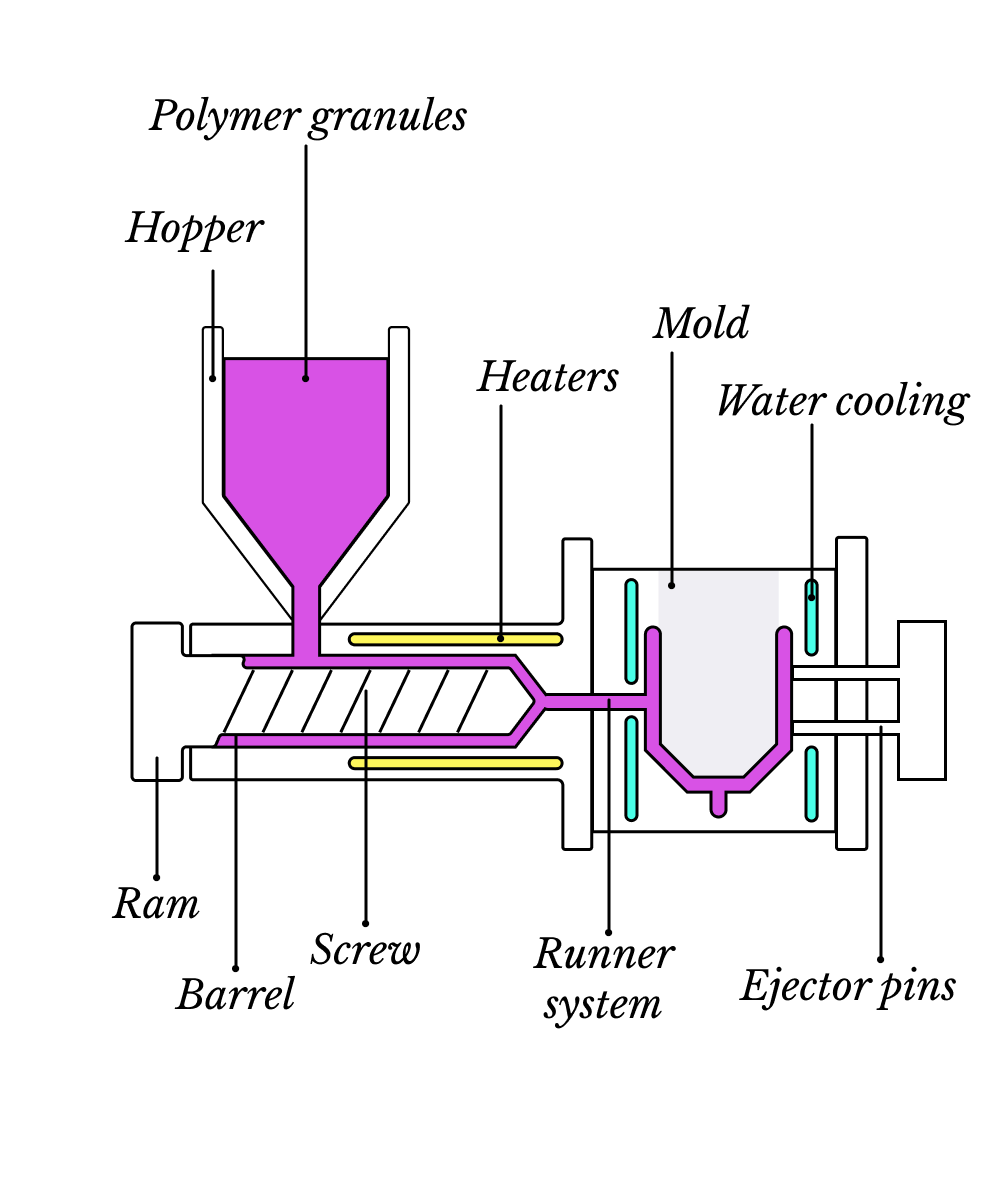
Conclusion
Finally, plastic injection molding works as a crucial production procedure that makes it possible for the reliable manufacturing of top quality my link components. Proficiency of the shot molding procedure, consisting of the understanding of materials and the influence of numerous variables on item quality, is essential for attaining optimal results. The advantages of this approach, such as cost-effectiveness and design flexibility, further underscore its relevance across multiple industries, strengthening its standing as a preferred selection for high-volume production.
Plastic injection molding offers as a foundation of modern-day manufacturing, providing a systematic technique to generating complex components with accuracy.Plastic injection molding uses a number of advantages, consisting of reduced waste, consistency in manufacturing, and the capability to include intricate designs that might be challenging with other making approaches (Plastic Injection Molding). As industries proceed my sources to innovate, plastic shot molding remains at the forefront, allowing the growth of innovative products that satisfy developing customer demands
The injection molding process is a sophisticated strategy that involves numerous crucial stages to create high-quality plastic elements.In conclusion, plastic injection molding serves as a crucial production process that allows the reliable production of top quality elements.
Report this page